对于苏州SMT加工多层板,钻孔是一种非常重要的工艺。下面将介绍一种高效的钻孔方法。
首先需要选择合适的钻头。在选择钻头时,需要考虑到多层板的厚度和孔径尺寸,并确保钻头质量良好,以确保钻孔的准确度和耐用性。
然后需要确定钻孔的位置和布局。在多层板上使用CAD软件来设计出钻孔的位置,确保各个孔位的准确性和均匀分布。
接下来是钻孔过程。将多层板放置在钻床上,并借助钻床的旋转功能以及合适的压力,使用选择好的钻头进行钻孔。钻孔时应注意保持稳定和均匀的切削速度,以免损伤多层板。
最后是钻孔的检查和修整。完成钻孔后,需要使用显微镜来检查每个钻孔的质量,并进行修整,以确保孔径尺寸和位置的准确度。
通过以上的钻孔方法,可以在苏州SMT加工多层板时达到较高的钻孔质量和效率。
多层印制板的钻孔过程中,由于板内铜层较多,钻头切削会产生大量热量。由于基材的热导率较小,热膨胀系数较大,导致钻头切削所产生的热量无法及时传导出去,从而导致钻头发热,温度迅速上升。钻孔壁会对钻头产生摩擦力,产生更多的热量,进而进一步提高钻头温度,甚至达到200℃以上。这不仅需要钻头施加更大的切削力,同时也增加了钻头的磨损。同时,在多层印制板基材中的树脂玻璃化温度要低得多,导致软化的环氧树脂会附着在钻头上,导致钻头在前进和后退过程中,污染孔壁内部的铜层切削面,形成所谓的环氧钻污。环氧钻污会影响孔壁铜层与内部导体的连接可靠性,必须完全清除。防止环氧钻污的产生和清除是保证多层印制板金属化孔质量的关键。一般来说,加工厂家从控制钻孔质量和清除钻污两个方面入手,既可以减少和防止钻污的形成,又可以对已经出现的钻污进行彻底清除,从而确保孔的金属化质量。
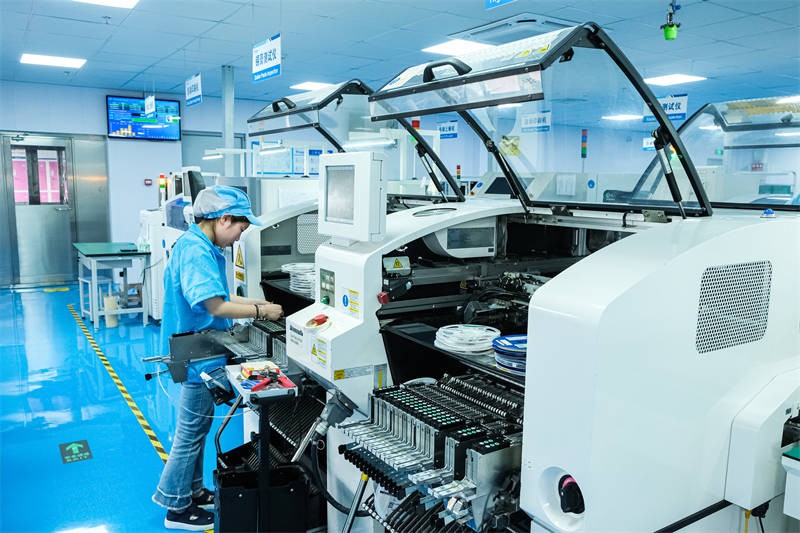
在多层板钻孔过程中,可能会出现孔口毛边、孔壁粗糙、基材凹坑及环氧树脂钻污等问题,但可以通过改进钻头质量和钻孔工艺来解决。具体操作应遵循4.3节的钻孔工艺标准,主要是要控制好钻头的质量、钻孔数量和钻孔参数。一般而言,多层板的层数越多,同一个钻头要钻的孔数就要减少,而钻孔的孔径越小,钻头的转速就要提高,同时还要注意合适选择钻孔盖板和垫块。